Inspiration/where it all started...
Lots of ventures start by accident, and Recycling Technologies (RT) was no different. In undertaking a consultancy project for Warwick University in 2010, Adrian Griffiths bumped into the reality of how little plastic is recycled. Like most people, he thought that waste plastic was collected in boxes or bins, taken away and recycled back into more useful plastic – bottles becoming more bottles. While completing the market research for the university it became shockingly clear how little ‘bottle-to-bottle’ recycling was being done, leading to the question ‘how can we do more?’.
Working with professors Jonathan Seville and Jan Bayens, a scheme was outlined to use a fluidised bed reactor into which plastic was injected continuously to undergo thermal cracking or pyrolysis. Gradually the project was extended to Birmingham University and became a collaborative summer project for two students. Environmental Integrated Services were drawn into the project to help develop the mass and energy balance. Before long, local business angels were successfully approached to help fund the building of a bench scale rig to test the conceptual design that was emerging. The Alliance for Cartons and the Environment (ACE) provided some industrial funding, recognising the potential for the concept to deal with the polythene / aluminium layer within a carton. This support was pivotal, the seed funding was raised, and Recycling Technologies opened a small workshop, demonstrating that it was possible to recycle virtually all plastics back into oil.
Problem solved
Recycling Technologies is on a mission to accelerate the evolution of plastic into a more sustainable material. Currently, 88% of the plastic used in the world is either buried, burned or leaked into the environment. This means that the world recycles only 12% of the 260 metric tons of plastic waste produced each year. The recycling rate for low-grade plastics such as films, bags and laminated products is especially low due to how difficult and uneconomic it is to recycle them using existing mechanical recycling processes.
To address this problem, the company has developed the RT7000 – an innovative machine that recycles difficult-to-recycle plastics into an oil called Plaxx®, which can then be used as a feedstock for new plastic production. In doing so, the RT7000 provides the missing link between end-of-life plastic and the start of the plastic production chain, helping to ensure cradle-to-grave circularity for all plastic materials.
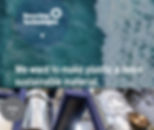
Long-term goals
By providing our RT7000 machine as a recycling solution to the plastics value chain, Recycling Technologies hopes to disrupt the plastics manufacturing and waste management system. We hope our RT7000 machine will complement traditional mechanical recycling processes to increase the recycling rate of plastic to 90% (up from the projected best-case-scenario of 50%) while decoupling plastic production from fossil fuels and effectively diverting plastic waste from being incinerated, buried or polluting our environment.
by Recycling Technologies CEO and founder: Adrian Griffiths